By Dr. William Oliver Hedgepeth | 10/01/2020
Designing products from recycled materials — such as plastic, wood, paper, glass and aluminum — has become a business that needs an engineering management component. While there are environmental benefits to recycling, there are also tangible improvements to a company’s investments in manufacturing and in its bottom line. Those businesses need to better understand the complexity and problem-solving tools that are available from the application of engineering management.
Recycling is much more than what you place in your recycle container. Recycling is a global business and is part of the circular economy. This recycling concept is tied to each person in our growing world population of about 7.8 billion. And there are many problem areas in recycling within the U.S. and our global partners.
Organizations such as the Reverse Logistics Association (RLA) are leading the U.S. effort. Circular economy organizations form the combined footprint for cross-linking recycling efforts from Asia to the U.S. to Europe. And there are many issues and problems that can benefit from the principles derived from the study and expertise of engineering management.
Forward Logistics Is What We Purchase from a Retailer
Forward logistics involves what we purchase from a face-to-face retail store such as Walmart and Target, an online retailer such as Amazon, or even from a local hot-dog stand. These products are available for the customer to select, purchase and use. If that product is damaged or does not work, it can usually be returned to the retail store where it was purchased. If that product wears out or is no longer useful, it can be thrown into a trash can or it can be recycled by a company that collects such waste.
Each state has a waste management authority that controls and manages the items collected as waste or recyclable. However, some items cannot be recycled, such as plastics bags, food residue, Styrofoam cups, electric cords, or large pieces of wood and metal.
The retail industry defines reverse logistics as returned merchandise which the customer does not want, such as seasonal or holiday items, overstocked items that just did not sell, or items that have been recalled from the manufacturer or the U.S. government.
The process of receiving returned items has a separate business plan and operations. Returned items must be recorded in an inventory database, just like items in a forward logistics retail industry. Then the returned item must be inspected, and each item must be catalogued and placed with similar returned items as part of a sorting process.
Once the returned item is verified as defective or broken, it is sent to a third party for repair or recycling. If the returned item is in perfect shape, it should be added to the current forward logistics inventory list and database.
Global Circular Reverse Logistics
Reverse logistics activities involve a complex of process especially when other nations are involved. Thus, the concept of the circular economy has evolved. Various countries are partners in harvesting key elements or raw materials from recycled products. The global aspect is part of a restorative economic process, even part of helping to define the human impact from climate change problems, solutions and meanings.
The “circular economy” is a generic term for a restorative industrial economic model. It stems from the idea that our systems should work like living organisms, processing nutrients that can be fed back into the cycle, hence the “restorative” adjective. This framework takes its inspiration from living systems and draws on a number of more specific approaches including biomimicry (mimicking nature), industrial ecology and cradle-to-cradle lifecycles.
Issues and Problems Today for Tomorrow
An ideal product lifecycle is a circular economy, a closed-loop system intended to eliminate waste while reducing pollution and carbon emissions with global effects. We demonstrate the closed loop system by comparing an open process system (Figure 1) with a closed-loop system (Figure 2).

Figure 1: Open Process System
As shown in Figure 1, we have the generation of an item, say a cardboard shipping box, such as the large box used to contain breakfast cereal boxes. Once generated, the cardboard box can also be used as a shipping container for several boxes of cereal. Once the boxes of cereal are removed, the shipping container cardboard box is then sent to the waste management landfill.
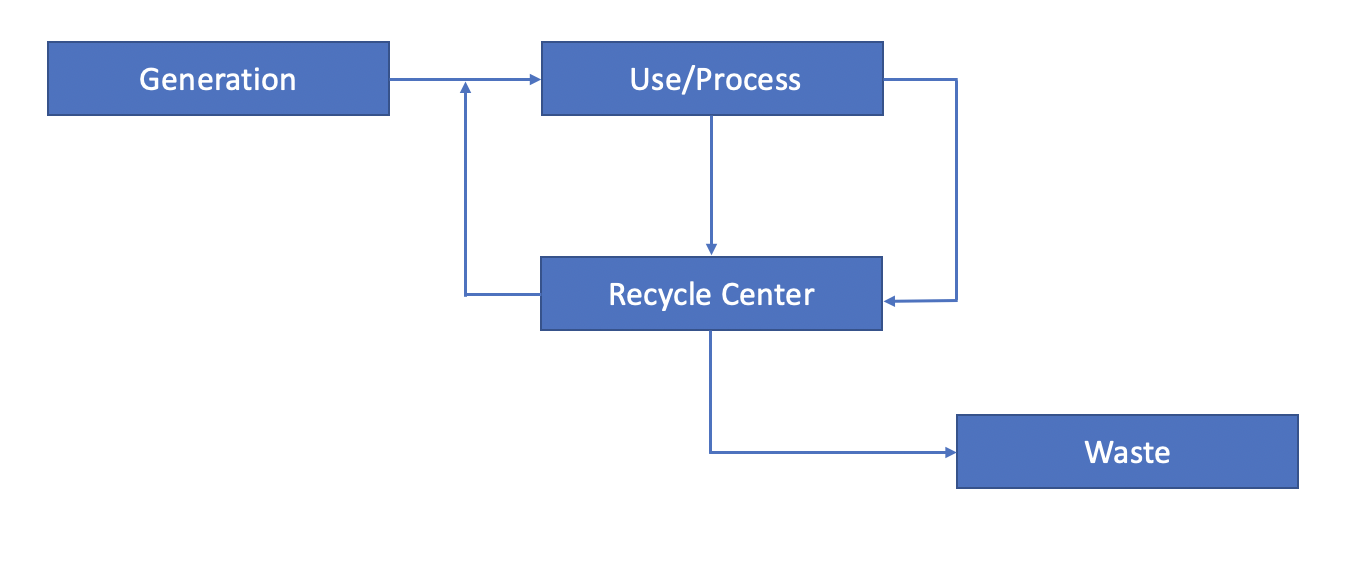
Figure 2: Closed-Loop System
In a closed-loop system, rather than sending the used container cardboard box to the landfill as waste, it is collected and sent to a recycling center. The recycling center reclaims the usable portions, mixes them with new components and then manufactures a new box.
Fundamentally, every step of the closed-loop system has issues and challenges. As an example, just the very fact of collecting the used cardboard box for recycling is a challenge. While recycling trends are increasing, over 50% of material is never sent for recycling.
There are many reasons why recyclable material is sent to the landfill rather than to a recycling center. Some of these reasons include people not taking the time or initiative to participate in the recycling system, a lack of available recycling centers, and even high costs.
An example of the high cost is trying to ship glass from Alaska to a recycling center somewhere in Florida. Shipping glass is costly due to the weight, packaging, and shipping methods, i.e. ship, air, truck or rail. When shipping costs are added to the recycling process, recycling becomes cost-prohibitive.
Six Sigman and Engineering Management for Logistics and Supply Chains
Six Sigma is a term used to define a series of steps and thinking about business problems. This term or process involves creating a diverse set of team members from the logistics or reverse side of a retail company or a company that manufactures supply items. The Six Sigma concept means to define, measure, analyze, improve, and control whatever process is helping to create a forward logistics flow of goods from a supplier to a retailer or customer, or the reverse logistics process. Understanding what the five processes mean is part of what engineering management is all about.
Now, one can earn a Ph.D. in engineering management. But for logistics and reverse logistics operations, some common sense may be all that is needed to define the current problem — for example, how this pandemic is having negative or positive effects on both sides of this logistics equation.
Six Sigma is a thought process that works toward a goal of reducing any variation in moving a product through its many supply chain steps and stops. What all logistics managers want is to improve control over any negative factors that can slow down or harm a product moving through a very complex chain of material handling events.
The term “Lean Six Sigma” is often used as well. It means trying to get rid of wasted human and machine efforts to produce products of high value as forward logistics, or to provide clean and usable recycled parts that can be returned to a manufacturing process as raw material.
The details of Six Sigma can be complicated. They have statistical factors to define such percentages of waste or average number of items to be analyzed. Statistics plays a key part in an inventory data base of finding the most efficient method to analyze the daily problems of forward and reverse logistics operations.
Bringing Six Sigma into logistics operations is due to the “unknown unknowns” created by the 2020 pandemic on all global and domestic supply chains. How critical are these unknown factors has not been established and may not be so until 2021. But, in the meantime, in order to improve and control the complexities of a global economic business, we must try to define them, measure them on current and projected operations, and then create some kind of solution.
Dr. Oliver Hedgepeth is a full-time professor in the Dr. Wallace E. Boston School of Business. He teaches and publishes on artificial intelligence, reverse logistics, and transportation and logistics. Dr. Hedgepeth holds a bachelor’s degree in chemistry from Barton College, a master’s degree in engineering management from Old Dominion University, and a Ph.D. in engineering management from Old Dominion University.
Dr. Hedgepeth’s first career was with the Department of Defense (DoD) and the Defense Intelligence Agency (DIA), where he was a mathematician and an operations research systems analyst. He has 28 years of computer programming and computer systems experience.